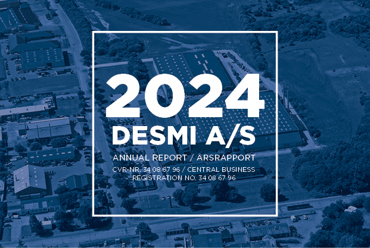
May 2025
March 2017
Removing toxic residues from power plant flue gases is as tough on equipment as it sounds. Known for having the toughest pumps in the business, DESMI is looking to take on more of the power plant challenge.
Powering forward
The world is gradually moving away from traditional energy production such as coal and gas and, as a result of the drive towards sustainability in recent years, waste-to-energy and biomass power plants have become a popular production method. Like their fossil-fuel colleagues, however, these plants must remove or ‘scrub’ potentially hazardous pollutants from the flue stage of the process.
The system requirements for flue gas cleaning depend on a long list of factors. Gas cleaning of complex flue gases can be realized in many ways, either in a few or several steps. Each plant is more or less unique, and must be evaluated separately to achieve an optimal solution.
Gas-cleaning systems can typically be categorised as solutions to remove:
In all cases, where there are highly-corrosive chemicals flowing through pumps 24 hours a day, a production facility is likely to face costly repercussions in terms of risk, productivity and repair if the machinery should fail.
Christian Busch, Danish-based industrial pump manufacturer DESMI’s sales manager for the utility sector across Europe, the Middle East and Africa, is very aware of the impact on machinery: “The ‘scrubbers’ are located after the boilers. Continued exposure to this combination of factors can rapidly have a detrimental effect on the pump machinery if it’s not specified and manufactured appropriately. We’ve spent more than two decades working with a very similar set of factors in pump supply to the maritime sector, and it’s partly from this that we got the inspiration to apply our technologies to land-based flue gas scrubbing, too.”
Coming ashore
DESMI’s expertise in supplying corrosion-resistant pumps to the shipping industry has received extra focus in recent times. Particularly following the introduction of more stringent regulations governing sulphur emissions. Now, the company is increasingly the subject of attention in the utilities sector, too, for the supply of efficient, reliable and durable pumps in the various stages of the wet scrubbing process.
“We have built our reputation on several aspects that are equally as important in the power generation industry as they are in the maritime world,” says Henrik Ottesen. “It’s the same formula, you might say, designing pumps fit for purpose and beyond, with reliability, efficiency, durability, ease of fitting and maintenance, and cost effectiveness as the key success factors.”
Over the past five years, DESMI has installed high-durability systems in power plants in its home market, and is now looking to extend its utility sales beyond the Nordic region with Henrik Ottesen at the helm. And there is clearly a need in the marketplace: “We’re focused on getting to know the big companies that specialise in making custom-built systems for the various power plants – and we’re discovering that they are just as keen to learn more about us.”
Hard-earned reputation
Quality of all components is obviously a key factor for both utility and manufacturer, especially when dealing with the processing and neutralisation of dangerously toxic chemicals. The pump units need to be particularly resilient to corrosion, they must be able to withstand continued load and usage over long periods, and they must ensure minimum down-time. The ramifications of taking a plant offline for essential pump maintenance due to malfunction or wear and tear can be immense – and commercially unacceptable. For these reasons, ultra-high quality pumps are an absolute must in such application areas, and DESMI’s centrifugal pumps in super-duplex stainless steel are well-suited to the task.
DESMI believes that the versatility, strength and support services of its product line makes it an ideal choice for turnkey and sub-system companies delivering to both large- and small-scale plant projects. As with all DESMI pumps at this level, service including replacement of bearings and mechanical shaft seal can be carried out without removing motor and piping, saving both time and money for the power plant, enabling utility staff to carry out service tasks themselves, and boosting uptime statistics.
Henrik is confident of DESMI’s ability to maintain customer satisfaction with its solutions: “Often, utilities require an extended warranty period, corrosion guarantees and fast customer service that can match such an aggressive, high-stakes environment. And that’s something we can definitely provide.”
With more than 100 years of heavy-duty pump development and manufacturing for a broad range of demanding applications, DESMI is likely to have a lasting impact on power generation infrastructure for decades to come.
May 2025
May 2025
April 2025
February 2025