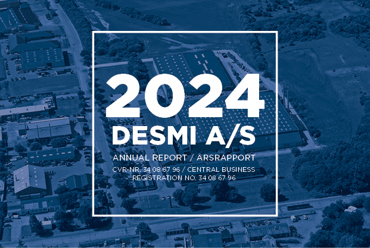
May 2025
January 2015
The concept of burning spilled or leaked oil on the sea’s surface has been known for many years, offering an extremely effective way of reducing the spill by as much as 90 percent with minimal equipment. The method, commonly known as in-situ or controlled burning, takes advantage of the fact that oil can be ignited on water if the layer is at least 3 mm in thickness – even under Arctic conditions.
Compared with mechanical clean-up, chemical dispersants and natural assimilation, in-situ burning is highly effective, particularly in remote areas where the resulting smoke plume isn’t so visible, or where it is difficult to deploy other types of clean-up equipment. Moreover, if properly employed, in-situ burning can result in the least detrimental overall impact on the environment.
Although these advantages had long been recognized, the true potential of in-situ burning could not be realized: the technology to do the job properly simply wasn’t available, and regulatory acceptance was slow in coming.
The journey begins
It wasn’t until the late 1900s, in fact, that the first steps were taken in a journey that would finally see in-situ burning emerge as a mainstream option. Numerous research efforts aimed at finding the most efficient burning means were conducted or commissioned by Shell Oil Company, Dome Petroleum and Exxon (now ExxonMobil), all with significant production in Canada and on the Alaska North Slope. These investments sparked a wave of new exploration into the development of durable, fire-resistant materials that could deliver on the promise of in-situ burning.
In 1982, a landmark Exxon Production Research project began to explore the technique of in-situ burning in earnest. At that point, the materials available for use were hopelessly inadequate. For a time, the best available practice was to take a conventional boom, wrap a multi-layer fabric “blanket” around it that could absorb as much seawater as possible, then light the oil and hope for the best. At some stage, however, a salt line or silt build-up could form in the material, allowing the fire to take hold and burn the fabric away – making the solution time-consuming and expensive to use. Despite various attempts to remedy such problems, the “water-cooled” model faced significant challenges.
A lack of standards
The lack of durable material wasn’t the only issue to be solved, however. The industry was also far from reaching agreement on appropriate standards for the equipment that would enable offerings from different manufacturers, for example, to be used seamlessly together. In short, much work needed to be done.
DESMI takes up the story: “Years back we got a call from Exxon, asking us to come up with a material that was not water-cooled, but which could handle the heat of the burning oil, and be able to withstand all the abuse a harsh environment like the Arctic has to offer.”
An early solution
By the late eighties, a company had come up with a hybrid fibreglass and wicking material wrapped in conventional fabric to create a redeployable, high-temperature oil containment boom. It worked comparatively well in tests, and large quantities were purchased for warehouse storage, mainly in Alaska. Due to the relative infrequency of spills or leaks, however, there were very few opportunities to properly evaluate the boom’s real-life performance.
In the meantime, industry participants working within the 30,000-member standards organization ASTM International developed standards for conducting in situ burns, for assessing expected lifetimes in simulated environments, and for developing products. The United States Coast Guard, for example, sponsored projects to test a range of booms in large tanks. Finally, a range of standards were developed that were to prove invaluable in assisting the simplicity and cost-efficiency of deploying in-situ burning equipment.
PyroBoom®
Derived from the work begun at Albany International, the fireboom product Applied Fabric Technologies, Inc. (later merged with DESMI, itself a global leader in oil spill clean-up equipment) finally came up with was dubbed PyroBoom®. PyroBoom® is essentially a highly fire-resistant oil spill barrier that utilizes a unique, woven blend of refractory yarn and metallic materials to yield a fabric to which a polymer coating is then applied. Flotation is provided by a series of stainless steel hemispheres, containing a high-temperature resistant, closed cellular material. The fireboom’s proprietary Inconel/Fiberfrax® refractory fabric with its silicone coating has been tested to withstand repeated burnings at temperatures up to 1315°C/2400°F without catastrophic failures.
From the outset, PyroBoom® was designed to be simpler to use than existing firebooms that were known to be complicated to use, requiring extensive training and practice. Worse still, competing products quickly became water-logged, with dramatic weight gain that made subsequent retrieval difficult, and drying, storage and maintenance virtually impossible in field conditions. PyroBoom®, on the other hand, requires no external accessories or cooling pumps, and is far lighter so as to enable easier handling.
Firebooms to the rescue
PyroBoom® got its first big break – and a chance to show what it was really made of – when the Deep Water Horizon disaster struck in 2010. The call went out for clean-up equipment around the world, including in-situ burning booms. DESMI joined the effort, with PyroBoom® playing a key role as in-situ burning helped to greatly reduce the amount of oil hitting the beaches and marshes.
“Our product really shone. The guys doing the in-situ work got maybe two to three burns out of the old firebooms before it all had to be thrown away after a couple of weeks at best,” says DESMI. “In fact, out of the four fireboom products brought in, only two performed to any reasonable level. And that was despite trialing various ways of towing the boom, different sea conditions and so on.”
One of the two booms to prove most reliable in use was the PyroBoom®, standing strong even when subjected to repeated burns during as much as 4 days of 24 hour immersion. And it was this product that won the lion’s share of re-stocking among the various organizations around the world who had supported the clean-up effort.
“Beyond the fact that the material is so durable, it seems to be the simplicity of the PyroBoom® that makes it so interesting,” says DESMI. “It’s handled and operated like an ordinary boom, works in any environment and there are no pumps or maintenance to worry about.”
Despite having the leading product, DESMI isn’t resting on its laurels.
“The material itself is very robust. But going forward, we’re looking at ways to make PyroBoom® work more efficiently, working with several organizations to come up with more efficient ways to increase sweep speed and extend the useful lifetime. We are also examining safety aspects, aiming to mechanize handling so as to remove any risks there might be in manual procedures.”
DESMI’s R&D team is looking at ways to improve burning results, too – whether in-situ or in conjunction with skimmers. A key issue is the need to broaden the current operating envelope: presently, in-situ burning can be undertaken in a relatively narrow range of weather and sea conditions.
“During the Deep Water Horizon cleanup, we had relatively calm conditions,” says DESMI. “And, because the disaster was a blow-out, there was fresh, thick oil every day. That made it perfect for a fireboom solution, which was highly economical in comparison with mechanical recovery.”
Environment
Since clean-up operations, no matter which technique is used, are all about protecting the environment, the idea of a burning oil slick with a thick, dark cloud of smoke entering the atmosphere may appear counter-productive. Here however, DESMI is quick to point out the relatively positive environmental effects of in-situ burning:
“A lot of work has been done on the content and effects of the smoke cloud. We’re just creating soot, which is straight carbon. It looks nasty, but it goes away quickly and the smoke plumes aren’t as large as you might think. We’re effectively eliminating almost all of the toxic constituents, for the most part leaving only solid carbon, carbon dioxide, carbon monoxide and a minor amount of liquid oil when the day is done. The products and residues of the combustion are a very small fraction of the initial spill. They usually float, and can be recovered mechanically after burning.”
Slow but steady progress
With the Arctic region playing host to a growing number of vessels and offshore platforms, DESMI’s efforts to further refine in-situ burning are crucial to protecting the future of the local environment and wildlife. But advances in the market for fireboom equipment and techniques are few and far between. The problem, according to the DESMI team, lies largely in the fact that, thankfully, major accidents are uncommon, low-probability events.
“The problem in the oil spill industry is that it can take a very long time for new ideas to come to market – and even new, disproven ideas take time to leave. With Deep Water Horizon, ideas came out of the woodwork that had been shown to be bad ideas back in the seventies. Now they have resurfaced all over again and they’re still bad.”
With oil spills hardly an everyday occurrence, and few players as seriously involved as DESMI, the pace of technological development is slow. Every new event raises the level of interest for a period of time, bringing fresh people into play who, according to Peter Lane, don’t have enough experience in the industry to realize that many of their ideas have been unsuccessfully tried before.
Thankfully, there are a number of organizations in or around the oil industry that front up with R&D funding aimed at evaluating new concepts for in-situ burning and bringing the best of these to a commercial level.
Hearts on fire
“We’ve been involved in in-situ burning almost as long as it has been a concept,” says DESMI. “We’ve developed products and operating techniques, and played a big role in setting standards. It’s second nature to us – and we feel we’re doing something that can really make a difference.”
May 2025
May 2025
April 2025
February 2025